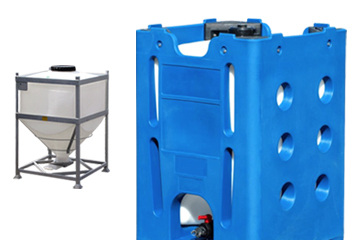
Products
See the full range of high specification IBC's and Drums for both dangerous goods and general purpose applications.
We employ the rotational moulding process to make all of our plastic containers. Rotational moulding is a casting process with no pressures involved, and it therefore produces effectively stress free mouldings that have no seams or welds.
In comparison blow moulding, used to produce many plastic drums and IBCs, involves vertically extruding a tube or parison of polymer, which is then clamped into the mould before being blown or stretched out to the mould shape. The result is a stretched polymer skin welded top and bottom.
Rotational moulding has other advantages when producing containers. Wall thicknesses are relatively even, with thickening in corners and radii, where heavy wall construction is an advantage. Typically blow mouldings are below 2mm in thickness. Our containers are 3-5 mm in thickness and can be more for demanding and abrasive applications.
The rotational moulding polymers we use are highly UV stabilised for long term outdoor sunlight protection and incorporate high levels of anti-oxidant.
Blow moulded polymers rely on colour pigments for UV protection and contain low levels of anti-oxidant. When we do choose to colour our mouldings we can incorporate low levels of pigmentation to provide translucency and site of contents. We can also cost effectively produce very low volume runs of individual colours since, unlike blow moulding, we don’t need to purge our machines between colour changes.
If you are looking for tough mouldings which will last many years outdoors, even in harsh environments, rotational moulding is the process to use.
Find out more about our range of IBC and drum products here.